Limiting factors in hygienic water distribution systems
Abstract
Every pharmaceutical manufacturing facility requires a pure water supply, which enables the chemical and/or microbiological quality of the water used in production to be carefully controlled. Various pure water grades are used universally in product manufacture and pharmaceutical processing.
In many cases water is often part of the product itself, and in others pure water might be a process intermediate, or used for equipment washing or cleaning of vessels and facilities for example.
The typical and common bulk grades of water employed are Purified Water (PW) and Water for Injections (WFI) which are compendial grades described in all Pharmacoepias, even though their origins and qualities can vary slightly. As a result, each pharmaceutical facility, whether it is manufacturing bulk API, secondary products, steriles, non-steriles etc is likely to have at least one pure water system within its suite of critical utilities.
Pure Water Systems
Pure water systems may be considered to consist of two distinct parts – the water purification stage and water storage/distribution. Over the past 25 years or so, little technical advancement has been made in pharmaceutical water systems overall. The possible exceptions are the introduction of new water purification technologies such as electro-deionisation and perhaps the increasing use of ozone as a water-borne, residual sanitant in storage/distribution systems. Both of these developments have been largely driven by vendor companies who have made advancements and improvements to their equipment through their own R&D programmes, rather than by system users or by the pharmaceutical industry itself.
It is relatively easy to purify water to the required pharmaceutical grades by a variety of reliable and established techniques such as ultra-filtration, reverse osmosis, electro deionisation, distillation etc and many combinations of these with other pre-treatment processes. However, maintaining this quality within the storage tank and piping delivery system to the user points can be more challenging. For example, the maintenance of microbiological water quality within an ambient Purified Water system relies heavily upon the design, engineering and operation of the storage and distribution stage. Despite this, there has been little or no fundamental development in the storage/distribution stages of pure water system in recent times. Today’s standard hygienic piping configurations employ stainless steel ring mains which are constantly recirculating throughout facilities. User offtakes branch from these loops as they pass by the relevant user points one by one in a series.
Function of the storage and distribution stage
The fundamental purpose of the storage/distribution system is simply to store pure water in a suitable tank or vessel, and to distribute it via ‘hygienic’ plumbing to all user points in the facility and maintaining the same consistent water quality. Whilst this is a simple objective, it is not necessarily easy to achieve, particularly in large buildings with a high number of user offtakes and involving long lengths of pipe work.
One of the main constraints of current distribution systems is the hydraulic limitations of the piping system in its ability to satisfy all user demands, to maintain adequate flows and pressures under all user conditions, and to sustain consistent water qualities at the user points at the same time.
Lack of ‘diversity’
Typically, conventional water piping systems form one or more constantly recirculating ring mains around the facility from the pure water storage tank. Each user point branches from the recirculating ring main (with a minimal ‘dead leg’) to serve each offtake point.
This is a relatively easy system to design when all user points are closed. However, designers must compromise flows/pressures etc if they are to consider all the possible permutations of user points that may be opened simultaneously, in any combination and configuration. The pump and pipe diameters are fixed in any one system design, and these become limiting factors to the operational flexibility of the system in most cases, although this can be mitigated to some degree by more sophisticated designs employing variable speed pump drives.
The outcome is that in maintaining acceptable flows and pressures, many system designs will only allow a few offtakes to be used together at any one time, giving rise to very low diversities. (Diversity is defined as the percentage of user offtakes that can be opened at any one time.
This is a serious constraint for production users and to manufacturing efficiency in many cases. Alternatively, systems may provide higher numbers of offtakes to be used at the same time, but to do this they must become ‘over-designed’ and inefficient. This effectively means that they must employ larger pumps and pipe diameters to cater for the occasions when many users demand water simultaneously.
Many facilities operate ineffectively and inefficiently (1) as a result of the conventional, stainless steel, recirculating pure water designs employed, and many have to compromise and curtail manufacturing activities because of their pure water system delivery constraints. These constraints and limitations have become accepted as the norm for conventional system design.
With current pressures upon manufacturing efficiencies and business performance there is a definite need to improve the delivery performance of pure water systems.
(1) Based on observations of the author, acting as an independent advisor, over 25 years.
Rigid design, fixed and inflexible operation
In addition to the significant hydraulic design compromises and inefficiencies of flow/pressure delivery of recirculating loops as described above, there are many other problems associated with conventional recirculating ring mains which render this design approach unsuitable for 21st century pure water systems.
A major limitation of the stainless steel recirculating ring main is its inflexibility. This means that from day one, all user points must be catered for, and user demands are translated into pipe sizes during the design stage accordingly. Should there be any future changes in requirements, i.e. a need for more offtakes, or for user points to be removed, or user positions to be changed, then it is quite likely that the original system might not be adaptable in meeting these new demands. Even if it is hydraulically possible to meet a new demand, production normally has to stop whilst the ring main is being modified, and with revalidation this could be for a week or longer. This is clearly a disruptive and expensive procedure. This inflexibility of water system design can have a detrimental impact upon the expansion, growth and development of a facility.
All 21st century manufacturing facilities have to be capable of modular build, and flexible adaptation to meet changing production demands. Currently, conventional water systems do not meet this requirement.
Rigorous and costly installation
Further, the installation of hygienic stainless steel ring mains is a rigorous process which is both costly and time consuming, and quite disruptive to operational facilities.
Polished stainless steel tube and fittings are welded together in-situ by an automatic, autogenous welding process known as ‘orbital welding’. This results in the welding process being carried out in areas which may need to be decommissioned from a health and safety point of view. This welding process is also difficult to perform, and requires an inert gas (argon) to be purged on both the inside and outside of the tube as the weld is made to prevent oxidation of the weld zone. This involves the ‘plugging’ of installed sections of the loop with dams, to trap argon gas during welding. Evidence of complete purging (ie absence of oxygen) in the pipe is required before welding can commence. The result is that only a few welds can be made in a working day, and the installation of welded, stainless steel ring mains often takes several months. The facility may need to be closed, or severely curtailed whilst this installation process is going on.
Should there be any future changes in requirements, i.e. a need for more offtakes, or for user points to be removed, or user positions to be changed, then it is quite likely that the original system might not be adaptable in meeting these new demands.
Onerous and extensive validation
In addition to these practical difficulties, there is an onerous and extensive requirement to qualify and certify the welding of the stainless steel loops. This requires a material certificate for each length of tube, fitting, tee, elbow etc, which requires full traceability and quarantined storage and handling of all of these materials. In addition, each welding machine and welder must be qualified and certified, and daily test pieces for each size of tube are normally required before the days work commences.
After the welds are complete, there is normally an inspection process carried out which may be visual via boroscope, or other more complex NDT process such as X-ray on each weld. This inspection criteria leads to an extensive and expensive qualification/validation process for the installation of stainless steel welded ring mains – which of course means very high cost.
Rouge
‘Rouge’ is a phenomena being increasingly observed and reported within the industry. Basically, it is ‘rusting’ of the stainless steel, producing red/brown deposits and stains upon many internal parts of the pure water piping system, including exits points into processing vessels and production equipment.
This is a concern both for manufacturers (GMP and QA procedures) and of course, of interest to the regulatory bodies.
Nearly all instances of ‘rouging’ seem to relate to hot WFI systems operating at elevated temperatures of around 80ºC, but nevertheless, a significant and increasing problem for pure water systems generally.
After construction of a new pure water ring main, the finished loop is conventionally degreased and passivated by the circulation of aggressive chemicals such as nitric or chromic acid at elevated temperatures. This is to pre-condition the weld zones prior to use of the system, in an effort to minimise ‘rouge’ formation. Despite this, initial passivation is frequently not effective in preventing the appearance of ‘rouge’, and it continues to appear in pure water systems deriving from stainless steel, without any effective remedy at present.
Conventional stainless steel ring mains – a limited performance
Whilst the limitations and constraints of conventional stainless steel ring mains have been outlined above, they seem to have been accepted and perpetuated within the industry, presumably because there is no understanding or appreciation of the existence of a better system. All of the constraints and limitations of conventional loop designs mentioned here are tolerated on a daily basis. However, the current pressures on the pharmaceutical manufacturing industry mean that this situation is unacceptable for the future, and there is a need to implement a better system solution now.
Examples of poor conventional loop performance
In 2001, as specialist water system design consultants, Honeyman took a step back from this convention and looked at pure water distribution from a completely different angle. Most of the user limitations and constraints of conventional systems arose purely because of the arrangement of user points in a ‘series’ manner. This meant that as taps were being opened, one by one, they added more and more demand to the ring main; and there came a critical point beyond which either the pump could not cope or the pipe work was simply not big enough for the duty.
Beyond this point, the next tap to open would simply ‘flatten’ the system, and the desirable flow/pressures could not be maintained. This could have potentially quite serious consequences. A case springs to mind when Honeyman were asked to investigate the appearance of frothing and foaming in a WFI vessel. Investigation revealed that the source was a small equipment wash sink, where the operators had a hose running from the WFI tap outlet into a sink full of soapy water. If this tap was opened when an excess of loop users were on-line, then a partial vacuum was created in the loop which actually ‘sucked’ soapy cleaning water from the sink into the WFI loop. This was the reason why the WFI vessel was ‘frothy’, and somewhat of a QA headache for the company ensued as a result!
Another GMP and regulatory related example relates to a cleaning validation issue. Extensive validation of the cleaning of a manufacturing vessel had been carried out. It came to light later, when validating the cleaning of a new vessel on the loop that the flows and pressures of cleaning water were highly variable, and dependent upon which other loop offtakes were running at the time.
Flows and pressures were found to be highly variable, as can be quite common with these pure water system designs. This unpredictability of pure water service meant two things. Firstly, the original cleaning validation that had been done was invalid – it was not reproducible. Secondly, it was very difficult to properly perform any acceptable cleaning validation with water from the pure water loop unless its pressure and flows could be stabilised and controlled under all operating conditions. This is an inherent problem associated with pure water ring mains, and an issue that many validation teams struggle with in terms of cleaning validation.
This is an inherent problem associated with pure water ring mains, and an issue that many validation teams struggle with in terms of cleaning validation.
What is the alternative to a conventional recirculating loop design?
When looking critically at the problems and limitations of recirculating ring mains, as outlined above, it soon becomes obvious that inherent difficulties lie in the arrangement of offtakes around the loop in ‘series’ connection. This means that the pump and piping design must be compromised, and flow/volumes add together cumulatively in the calculations.
Very soon the designer is restricted by a critical ceiling point.
At this point, the options are;
a) to restrict the number of offtakes that can be opened at once, or
b) use a bigger and/or variable speed pump and/or
c) install larger bore pipework to cater for sudden bursts of demand.
However, even these limitations provide only a partial remedy. None of these options will help with the other problem of adding, removing or just simply moving an offtake point when the system is live – which remains a headache for the life of the conventional loop system.
All of these problems, constraints and limitations can be removed simply be utilising a ‘parallel’ user offtake arrangement.
Parallel distribution of pure water
Quite simply, each user point is supplied from the tank with its own, individual recirculating loop from a central distribution skid in the plantroom. This system maintains all hygienic flow and pressure conditions to each offtake independently, whether the tap is open or closed. In the HydroGienic® parallel system, users are connected independently as and when required, via their own, individual recirculating mini-loops as illustrated below:
Constant recirculation takes place between skid and vessel in the plantroom, even when there are no offtakes connected
The advantages and benefits of this parallel distribution system are significant -:
• User points can be added, modified or removed whilst the rest of the system is left running, and production may continue during the modifications
• Modifications are easy to perform in a ‘plug and play’ fashion, with no production disruption and minimal validation effort
• The system can be installed with no users connected, and they can be added as and when required giving a totally modular build capability and unique flexibility
• All taps can be opened simultaneously without detrimental pressure or flow effect to deliver 100% diversity, due to innovative design within the HydroGienic® skid
• All flowrates and pressures are fixed as designed – there is no variation due to other user offtakes opening/closing simultaneously
• The flexibility and easy modification capability leads to low lifetime cost of ownership
• The low amount of water recirculating when user taps are closed leads to a more energy efficient system
Use of PTFE, small bore hose
An obvious feature and potential downside of the parallel arrangement is that there is a significant increase in pipework lengths within the distribution system compared to a conventional loop. Clearly, if this pipework was to be installed in orbitally welded stainless steel as in a conventional system, the benefits of parallel configuration would soon be overtaken by the disadvantages of pipework installation costs and complexity.
Closer examination reveals that conventional loop pipe diameters (typically from 1” to 3” or even 4”) arise purely as a function of the series arrangement, where a total flow requirement is calculated from the sum of all of the individual offtakes. Upon closer examination, it soon becomes apparent that the instantaneous flow demand at each individual offtake user is relatively low.
It therefore follows that the pipework needed for a parallel system needs only to be sized according to the single offtake served. The parallel arrangement means there is no summation of flows from offtakes calculated within the pipe diameters.
In HydroGienic® systems therefore, typical diameters would be in the ¼” to ¾” range – significantly smaller than conventional piping. These small pipe diameters may be effectively and easily served by alternative materials to welded stainless steel, ie the use of PTFE hoses. PTFE hose is a material which is widely accepted and used within the pharmaceutical, food and dairy industries, and complies with all of the standards and requirements for such applications.
Advantages of PTFE hose over welded stainless steel
PTFE hose provides significant advantages for pure water distribution applications at all operational temperatures and pressures, and under all typical sanitising conditions both thermal and chemical.
It is a very cost effective and elegant solution for parallel delivery ie :-
• Quick and simple installation – akin to a cable laying operation
• Certification and qualification of the installation process is simple and straightforward – effectively one piece of paper per hose, which may be 100 metres or more in length.
• No ‘hot working’ in production areas, minimum disruption to facilities and low production downtime
• No requirement for degreasing and passivation
• Reduced risk of rouge formation
• Significantly exceeds all temperature and pressure requirements of any pharmaceutical water applications (Operating temperature c 230ºC, pressure > 200 barg)
• Is compatible with all common sanitants
• Meets all regulatory and cGMP criteria
The powerful combination of parallel offtake configuration and employment of small bore PTFE hoses forms the heart and essence of the HydroGienic® system. Both of these features bring a unique set of advantages and benefits to system owners and users, as has been outlined above. The ‘plug and play’ versatility of adding and removing user offtake points, the ability to maintain 100% diversity under all operational conditions, and ability to provide a truly modular and flexible pure water delivery system are just a few of the headline benefits.
The HydroGienic® system also provides benefits to water system project planning and facilitation. Much of the construction of the distribution system can be carried out off-site, up to and including commissioning and FAT of the skid. This means that a new water system, comprising purification system, storage vessel and distribution skid can be delivered fully validated to site, even without any offtakes being connected. Offtake users can be added to this pre-validated system as and when required to enable a truly adaptable and modular system installation to take place.
The project also has the ability to adapt to changing user requirements, as invariably seems to happen during the installation phases. Of course, none of this flexibility or versatility is provided by a conventional stainless steel ring main. Once a conventional design is committed, then it is not easy to make any adjustments or modifications, and hence why the constraints of conventional loop systems may be something the industry can no longer accept.
A neat HydroGienic® user point with hoses tucked neatly inside a stainless steel sleeve for ease of cleaning within the production area – a wide variety of user point configurations and offtake terminations are available to suit all applications.
Summary
It is clear that there are many inherent limitations and constraints in conventional recirculating ring mains used for the distribution of pure water. This article has explained many of these such as;
- the lack of flexibility and diversity,
- likelihood of variable flows and pressures,
- expensive and time consuming installation and qualification,
- rouging risk etc,
which makes these systems unsuitable for modern, 21st century manufacturing facilities. Until now, these systems have been installed as convention because of the lack of a suitable and a better alternative.
All of the limitations and constraints of conventional systems have been addressed and solved by the innovative and proven HydroGienic® system.
The industry needs to recognise the problems associated with conventional pure water ring mains, then learn to understand and appreciate what the true advantages and benefits of parallel distribution can mean for production efficiencies and facility management in the 21st century.
The performance and cost savings achieved by the innovative and proven HydroGienic® system are unparalled:
- Reduced downtime: User points can be added, modified or removed whilst the rest of the system is left running, and production may continue during the modifications, thus reducing unnecessary process downtime
- Low lifetime cost of ownership: HydroGienic® is modular and “plug and play” in design, allowing for easy and cost effective modifications to the location or number of user-points, leading to low lifetime cost of ownership
- Guaranteed flow rates at all user points: All taps can be opened simultaneously without detrimental pressure or flow effect to deliver 100% diversity, due to innovative design within the HydroGienic® skid
- Energy efficient: The low amount of water recirculating when user taps are closed leads to a more energy efficient system
- Upgrade or brand-new: HydroGienic® provides a viable solution for current water systems that need further upgrades or for complete new installations, whatever suits your needs
For more information on the HydroGienic® system or to speak to one of our consultants, please visit: www.honeymangroup.com/hydrogienic
Author: Trevor Honeyman CChem., MRSC, CSci
Chairman, Honeyman Group LimitedA chartered chemist, Trevor worked for Glaxo, Barnard Castle for 16 years, initially as an analyst then development chemist before being appointed to oversee the management, control and development of all of the site’s pharmaceutical water systems.
The dedicated water section he created, expanded throughout the 1980’s to provide technical support for pharmaceutical water systems throughout the Glaxo Group worldwide, and Trevor developed a wider presence and reputation in pharmaceutical circles for his experience and expertise in this specialised field.
In 1991, Trevor left Glaxo to set up Honeyman Associates, initially an independent consultancy pecialising in pharmaceutical water systems and training services. The business expanded with the formation of Honeyman Water in 1997, followed by Honeyman Sterilisation (1999).
The business was streamlined in 2003 by amalgamating the three companies into Honeyman Group Limited to provide the platform from which our baseline expertise in water and sterilisation systems was developed into broader areas of pharmaceutical manufacturing support
Trevor can be contacted on +44 (0)1833 690101 or trevorh@honeymangroup.com
Over the past two decades, the Honeyman Group has helped many clients with the design, installation, validation and maintenance of their PW or WFI water systems.
Whether your requirements are for contract work, one-off, project based or during peak demand, at Honeyman, we have you covered.
For further information and advice on Water and Steam Systems please browse our knowledge hub.
We understand the sensitive nature of processes and products, to discuss your requirements with one of our experts in a confidential manner, please contact us with your details and a brief introduction, so we can arrange a call back at a time convenient to you.
To Request Further Information Please Contact Us:
Contact UsOur Customers:
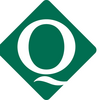
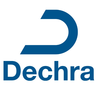

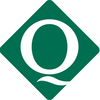
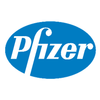

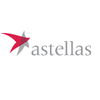
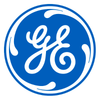
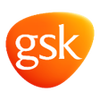

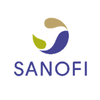

